The Materials of Sculpture
Sculpture is, loosely defined, a three-dimensional representation. Generally we think of sculpture as large objects, but the distinction on the continuum between smaller objects that may be treated as Decorative Arts to Statues to large scale architecture may be a matter of opinion, and the issues of conservation are similar. For example, the Collosus of Rhodes was a 108 ft tall bronze work that resided over the harbor at Rhodes until 226 B.C., when it was toppled by an earthquake.
While Greek and Roman statues in both marble and bronze most often come to mind when sculpture is mentioned, any material could be used for its creation. This includes Metals & Alloys, Minerals and Stones, Wood, Ceramics & Glasses, Polymers, and almost anything else imaginable in modern and contemporary Art as illustrated with a variety of examples below. The extent of variation in these materials used presents challenges for conservators in identifying and treating that wide range of compositions.
While the materials themselves have been treated on the specific pages given above, there are some topics specific to the use of those materials in sculpture. A major consideration for objects that are stored outside is the effect of exposure to the elements in alteration of the surfaces of the objects.
_439px.jpg)
Metals & Alloys
Objects made of metal are subject to corrosion, which is the oxidation of the metals often in the form metal oxides/hydroxides that may then flake off. This is a particular problem for objects containing iron, but other metals and alloys are subject to corrosion as well. Corrosion can be controlled by attaching a block of a more easily oxidized metal by a metal cable to a metal statue. This is known as galvanic inhibition of corrosion. Blocks of magnesium are often used for this purpose. The chemistry derives from the electrochemical potentials for the two metals:
Mg2+ + 2 e- → Mg(s) E° = -2.38V
Fe2+ + 2 e- → Fe(s) E°= -0.41V
Because magnesium is easier to oxidize than iron, electrons will flow from the magnesium block to keep the iron in its elemental form. The magnesium is consequently oxidized to Mg2+. The overall process can be written as:
Fe2+ + Mg(s) → Mg2+ + Fe(s) E° = +1.97V
Note that the more positive the value of E0 is for an overall reaction, the more favorable that reaction is.
A similar way to protect metal objects is galvanizing. In this process, the object is coated with a layer of zinc. The zinc serves as both a coating and as a galvanic inhibitor. Common metal objects like buckets are galvanized to extend their useful life. Of course, once the layer of protective metal wears off or is consumed, the the object is not longer protected.
Aluminum is a notable exception. Even though its standard reduction potential (E° = -1.68V) indicates that it would be more difficult to reduce/more easily oxidized than most other metals, aluminum objects are inert to corrosion. Unlike other metals, aluminum oxidizes easily on its surface but the Al2O3 that is formed is intimately bound to the metal underneath, forming a very durable protective layer that prevents further oxidation. On the other hand, this coating is amphoteric, a word meaning that it acts as both an acid and a base. Consequently, the aluminum oxide coating will dissolve in strong acids or bases, which will allow the metal underneath to react. Aluminum powder mixed with iron oxide is used to weld objects, such as the rails used in railroads, that are in remote locations. The mixture is therodyamically unstable but requires an initiator. Once it proceeds, however, it is extremely exothermic, producing Al2O3 and molten iron.
Metals are very durable and make long-lasting sculptures, but metals are also dense which poses engineering problems. Practically, only small objects can be made of solid metal. As objects became larger, the practice was to make the objects hollow to save both on expensive metal as well as to keep the weight of the object reasonable. Even hollow objects needed to be carefully engineered in order to achieve structural integrity of the object, especially if the object was not a compact shape. A small statue of the Budha would be relatively stable, but a large Greek statue of a hero with outstretched arms would pose challenges to keep the arms from cracking off under their own weight. Larger objects needed an artist that understood engineering as well as design.
The coinage metals are very malleable and can be beaten or rolled into sheets. This allows for production of objects by shaping and cutting the sheets into the desired shapes such as the copper sheets used to form the rooves of buildings or the external coating of the Statue of Liberty.
Another method of shaping metal was to pour the molten metal or alloy into a mold. This process could create either a solid or a hollow object, depending on how the mold was created. For complex objects, the statue may have been cast in smaller pieces which would then be assembled and welded together, followed by a smoothing and polishing process. Note that the Roman Portrait Figure of a Ruler shown below is hollow. An important technology was lost-wax casting. In this process an initial mould was prepared from a wax model of the object to be produced. This model was then coated with clay which was hardened, producing a negative image of the object. The wax was then removed by melting. Molten metal could then be poured into the clay mold to create the object. Originally, these clay moulds would have been destroyed to release the object, but later the moulds were created in sections so that the the mould could be opened and then later reused.
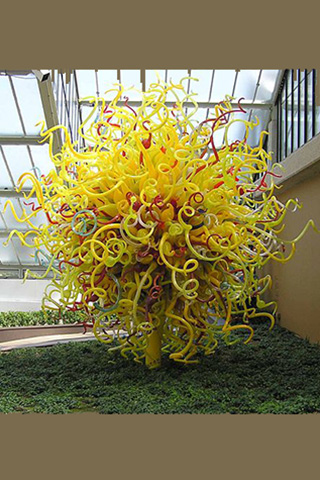
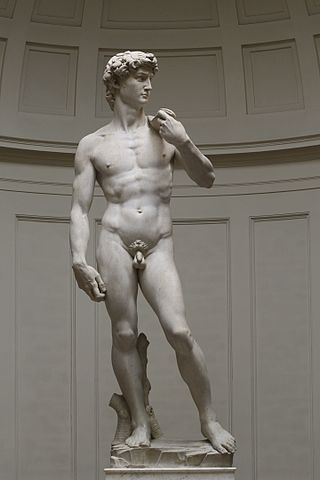
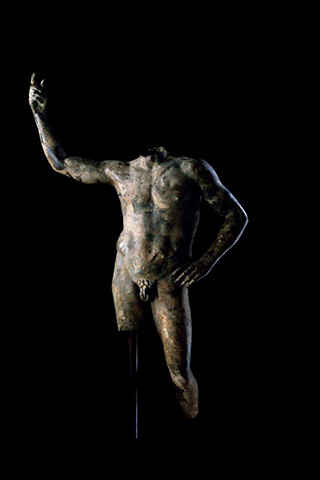
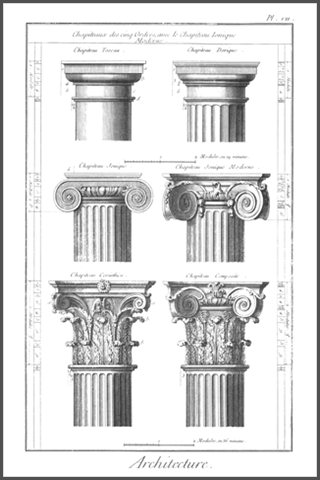
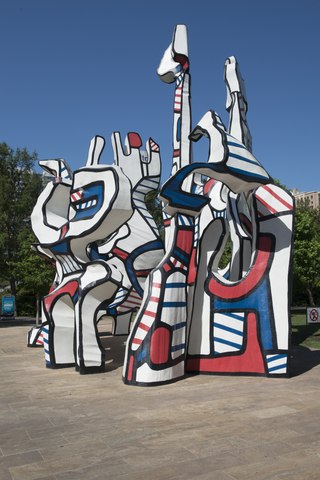
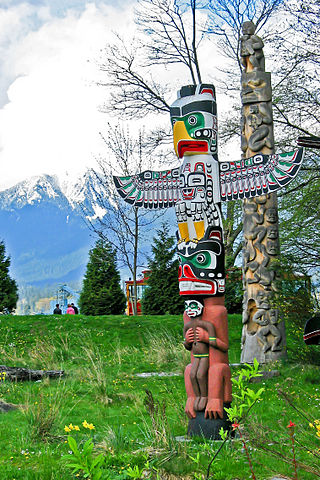
_342px.jpg)
Oxidation of the surface of copper-containing objects, including bronze evidences itself in the formation of patinas. The well-known color of metallic copper will turn to blue or green once Cu2+ has formed, the color depending on the other anions present. This patina is characteristic of objects that have had long exposure to the elements, and cleaning off the patina would decrease the aesthetic value of an object. During the restoration, it was determined that the patina was composed primarily of CuSO4·3Cu(OH)2 (brochantite)with some areas showing CuSO4·2Cu(OH)2, known as antlerite, [Matyi, Baboian, Powder Diffraction, 1986]. The latter is less stable and suggested that environmental acid exposure was affecting the patina.
Of course, oxidation processes could proceed so far that an object could lose structural integrity over time. This was a significant problem for the Statue of Liberty that had to be extensively restored due to corrosion. The Statue is composed of copper sheets attached to an iron framework. This was problematic because of galvanic corrosion, which is similar to the magnesium/iron interactions described above. The reduction potential of Cu2+ is +0.34 V, so copper in contact with iron would result in enhanced oxidation of the iron skeleton even though the iron would have been protected physically from the elements by the copper exterior. Originally, the contact between the copper skin was isolated from the iron framework by placing shellac-coated asbestos between them, but ultimately this failed, and the framework was replaced in the early 1980s by an chromium-nickel-molybdenum stainless steel alloy coated with Teflon®. See a short description of the restoration from the National Instiute of Standards and Technology (NIST) at Keeping the Lady with the Lamp Standing Tall.
Stone
The stone used for statues is also subject to weathering that will alter its surface. While all stone will be subject to erroding with exposure to the elements over time, the carbonate minerals (limestone, marble, alabaster, dolomite, etc.) are particularly sensitive because of the reaction of the carbonate ions with acid (see Gems & Minerals). The overall process releases CO2 and produces soluble Ca2+ or Mg2+ compounds. These weathering processes occur slowly over long time scales and are difficult to reproduce in modern objects, so examination of the surface composition of ancient stone statues is a standard way of assessing the age of the object.
CaCO3(s) + 2 H+(aq) → Ca2+(aq) + H2O(l) + CO2(g)
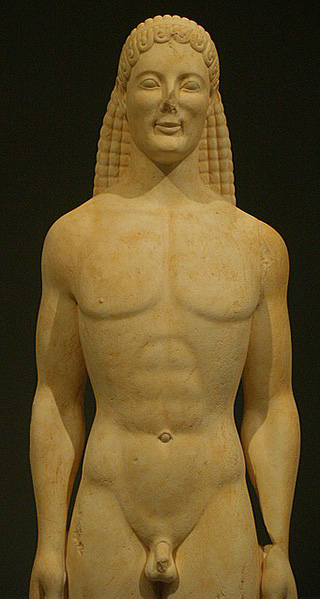
In the case of dolomitic marble, the composition of the stone contains both calcium and magnesium. While calcite is pure calcium carbonate, the mineral dolomite is CaMg(CO3)2. When magnesium is present, it is preferentially removed relative to calcium carbonate in a process known as dedolomitization. The surface consequently becomes richer in calcite (CaCO3) than the interior of the stone. Examination of the Ca/Mg ratio was one of the analyses performed on the Getty Kouros to attempt to establish its authenticity. This statue was purchased by the Getty Museum but its authenticity has proven controversial, and it has been extensively studied. Initially it was thought that the surface of the statue showed dedolomitization consistent with its proposed age. A complex procedure was developed in a laboratory to show how a forger could have achieved dedolomitization, but that procedure was so involved that it was thought highly unlikely that a forger could have reproduced it. However, it was later shown that the surface actually contained a layer of calcium oxalate rather than calcite. This could have arisen from the statue being buried, but treating the statue with oxalic acid, HO2CCO2H, would also have created such a surface. Oxalic acid is produced in many plants, and it would react with basic compounds such as calcite to produce a salt. (See The Getty Kouros Controversy, Part 3, University of Delaware). A link to the report produced by an expert panel that met in 1992 is found at Getty Kouros Colloquium.
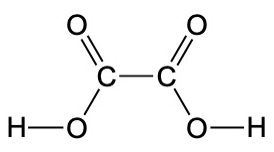
HO2C-CO2H(s) + CaCO3(s) → Ca[O2CCO2](s) + H2O(l) + CO2(g)
The Getty Kouros was also examined by measuring the 16O:18O isotope ratios in the marble, which is characteristic of marbles found in different quarries. The value for the Kouros was compared to other known marble samples and the origin of the marble was identified as the island of Thasos.
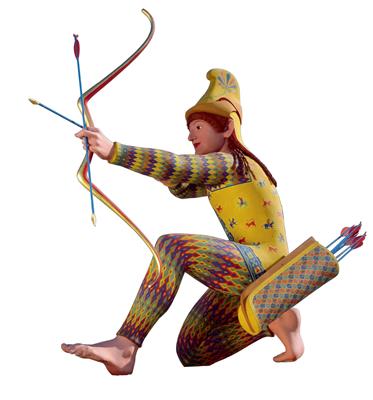
Examination of the surfaces of Greek statues has also revealed surprises. While most Greek statues, and their modern imitations, are depicted as being in natural stone, recent investigations have revealed traces of pigments indicating that the statues were once painted in bright colors. The British Museum has found evidence for this in statues obtained from the Parthenon. Matthew Gurewitsch in Smithsonian Magazine, July 2008, points out that Euripedes in his play Helen of Troy has Helen confirm the Greek practice of painting their statues with these words,
"My life and fortunes are a monstrosity,
Partly because of Hera, partly because of my beauty.
If only I could shed my beauty and assume an uglier aspect
The way you would wipe color off a statue."
Evidently, not only was coloring statues a common practice, it was also considered an integral part of the aesthetics of the sculpture.
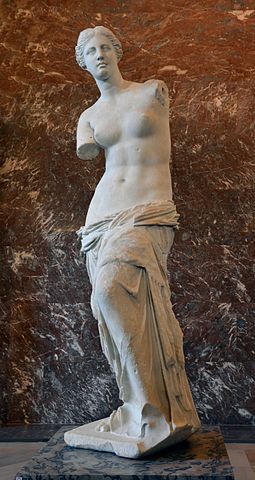
Stone objects are prepared by first cutting blocks of stone from rock quarries. Some rocks, such as sandstone or limestone, are fairly easy to cut with copper or bronze tools but more compacted materials such as granite were more challenging. The ancient Egyptians using only copper or bronze saws were able to cut granite by adding sand as during the cutting process. Essentially, the sand became the cutting surface and the copper tool was the instrument by which the sand was rubbed across the surface of the rock. This process has been described by a Nova special on the preparation of a Pharoah's obelisk. Once isolated, a stone block could be shaped using subtractive sculpture in which the stone is removed with chisels to produce the desired shape. Michelangelo used this technique to produce the Pietà and David. Notice that the design of David pictured above has both arms attached to the trunk of the statue as a way of stabilizing them. The tree stump behind David's right leg helps to stabilize the overall composition. Many Greek and Roman statues, such as the Venus de Milo pictured here, have missing arms and other appendages owing to their weight and consequent instability.
Stabization of large statues is also concern for museums in how these works are displayed and stored. It can be particularly challenging in areas prone to earthquakes. A YouTube video about the The Getty Kouros describes the engineering solutions displaying the kouros and presents a good analysis of the potential problems that need to be considered and some of the solutions to those problems. Regardless of whether the statue is real or a forgery, the video gives insight into how museums must treat such objects.
The cutting tools used by the sculptors also left marks on the surface of the statues. These marks can be examined and compared to those of known artists to establish authenticity similar to the way brush strokes are used to confirm authenticity of paintings.
Wood
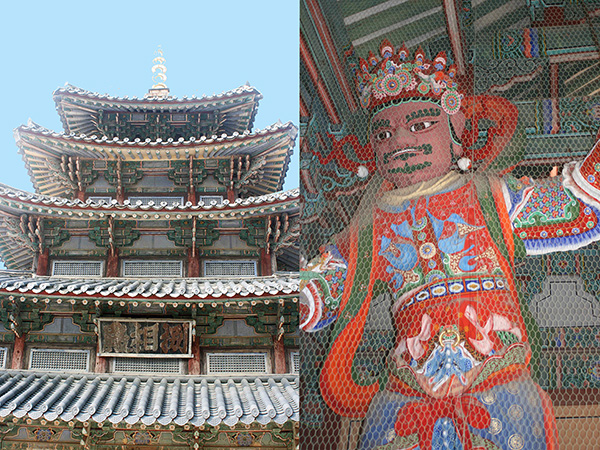
Like stone and metal, wood has been used for millenia as a material for buildings and sculpture. It is easy to fashion with simple tools. It can be sawn, drilled, sanded and carved to produce objects of all kinds. Unlike metal and stone, wood is susceptible to damage by insects and rot, especially if it stays wet. Changes in humidity can lead to cracking and warping. Nevertheless, many wooden statues have survived for hundreds or thousands of years. Egypt has a particularly rich history of wooden statues that have survived thanks to the arid climate. Included in this are the highly decorated wooden sarchophagi. But Egypt is not the only ancient culture that used wood. In Asia, magnificent temples adorned with carvings and wooden statues abound as seen in the figure of the Boepjusa Temple in South Korea. These buildings and the carvings that adorned them were made of elaborately painted wood. The paint helped to protect the wood from the elements and insects. See Wood for a detailed description of the tools used for woodworking.
Sunken ships such as the Vasa Warship that was recovered from the Stockholm harbor where it sank in 1628, have been carefully preserved. The ship could not be allowed to dry out, as this would cause major damage to the long-deteriorated cells within the wood. This problem was solved by displacing the water in the vessel with ethylene glycol, HOCH2CH2OH, whose boiling point is 197°C. Ethylene glycol has some properties similar to water but it does not leave the wood so readily because of its higher molar mass and lower volatility.
Glass
Glass is a less common material for the production of sculpture, but it has become more popular in modern times. Glass, of course, is easily cracked and broken, making such objects much less enduring. There are also challenges in making glass objects large. Glass is shaped by melting the glass and handblowing it, or blowing or pouring it into molds. After it has been worked, glass must be carefully annealed to remove strain. In this process, the glass is heated close to its melting point and allowed to cool very slowly. Small objects can be annealed by hand using a glass torch but this is not feasible for large objects where the heating and cooling would be uneven. The size of objects is limited then to the size of the annealing oven. For this reason, many large glass sculptures are made by assembling them from a number of smaller parts.
Shortcuts
Resources and References
- Report of the Getty Kouros Colloquium
- Getty Kouros Controversy, University of Delaware.
- An x-ray diffraction analysis of the patina of the Statue of Liberty, Matyi R J, Baboian, R, 1986, 1, 299-304; DOI: 10.1017/S0885715600011970.
- A genuine Dilemma: The Authenticity of the Getty Kouros.
- Paint on the Parthenon, conservation of ancient Greek sculpture, British Museum.
- True Colors, Matthew Gurewitsch, Smithsonian Magazine, July 2008.
- The Science Behind Saving A Sunken Ship - Conserving The Vasa Warship, Suze Kundu, Forbes Magazine, June 30, 2016.
Credits for the Header Image
- Portrait Figure of a Ruler, Roman,200-225 AD, Bronze, Museum of Fine Arts Houston.
- Ballplayer, classic Veracruz, ca. 600-900 AD, Earthenware with slip and traces of polychrome pigment, Museum of Fine Arts Houston.
- Bust of a Bacchante, Albert-Ernest Carrier-Belleusea (1824-1887), French, 1860s or later, Museum of Fine Arts Houston.
- Maquette for Personnage et Oiseaux (Personage and Birds), Joan Miro, 1893-1983, Spanish, Wood with polychrome, Museum of Fine Arts Houston.
- Companion Statue, Egyptian, 332-30 BC, Wood, Polychrome, Gold, Museum of Fine Arts Houston.
- Walking Man, Auguste Rhodin, French, 1840-1917, Bronze, cast 1962, Museum of Fine Arts Houston.
- Albero folgorato (Lightning tree), Giuseppe Penone (b. 1947), Italian, Bronze with gold leaf, 2012, Museum of Fine Arts Houston.
Department of Chemistry
Houston, TX
6100 Main St., Houston, TX 77005-1827 | Mailing Address: P.O. Box 1892, Houston, TX 77251-1892 713-348-0000 |